Pigment is widely used as a colouring substance for concretes, particularly in the sector of city furniture. It is successfully applied for coloured concrete floor tiles, paving stones, bordures, lemon-squeezers, park and garden tables made of concrete, benches, flowerpots which are all today's most fashionable elements of city furniture and also in the production of coloured roof-tiles, synthetic marbles and granite pigment is used with great success.
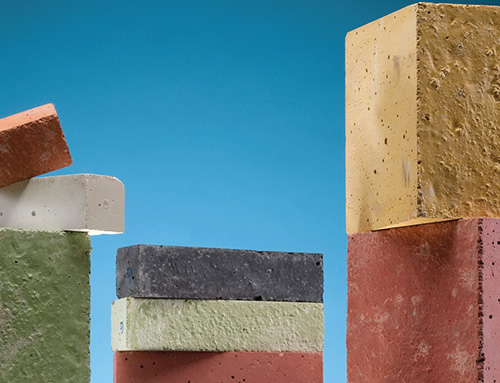
How to Choose Good Quality Pigments
The points to be careful with while choosing a good quality pigment are given below.
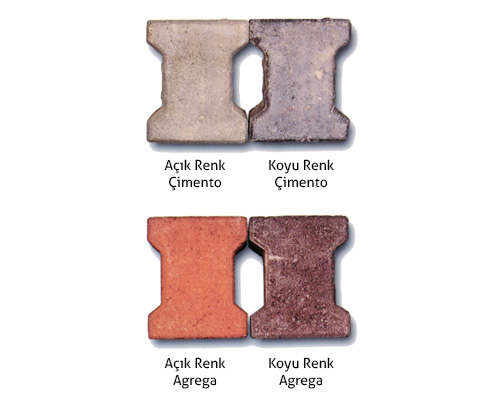
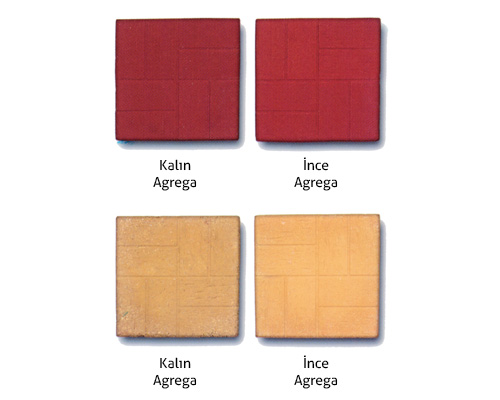
Structure of the flakes
The results obtained from scientific studies show that there is no deterioration on the concrete in which the pigment is used, provided that the use of inorganic pigment does not exceed the 5% of the total amount of the used cement. The structure of the flakes of the inorganic pigment which is used within the 5% affects the strength of the concrete. The inorganic Pigment which flakes are in a structure of needles causes an increase of the water absorption in the concrete and the strength of the concrete reduces. Pigments of spherical flakes do not constitute such problems. Thus, the use of pigments with spherical flakes for the strength of the concrete reveals the importance attributed to the quality.
Size of the flakes
In order for the pigment to become combined with the concrete mixture and reach every single point in the mixture, it should be as micronized as possible.
Power of colouring
The main weapon of the enterprises today is low costs regarding the working conditions under which the enterprises have to work by strongly competing with each other. The colouring power of the inorganic pigments that have been marketed in same quantities and same costs is an important factor in making a preference. The inorganic pigment with high colouring power will provide the desired colouring by a smaller quantity compared to the one with less colouring power for a production under the same conditions. Provided that other factors are equal, of the two enterprises which use same amount of inorganic pigment it is inevitable that for the one who prefers to use a pigment of high colouring power the amount of produced coloured goods will be higher, the costs will be lower and so he will be more successful in the market.
Dispersion
The dispersion and distribution power of the inorganic pigment which it is mixed into the concrete plaster will provide all the mixture to be coloured successfully. A pigment of high colouring capacity will penetrate through the concrete owing to proper dispersion and thus will obtain a perfect result. Besides the good dispersion factor, the mixture must be mixed for a certain required time. To add the pigment into the concrete plaster by sprinkling method while stirring the mixture is the best method used today.
Resistance against exterior factors
Fading of the colours, efflorescence and decomposition are the problems seen in concrete colouring. The colours cannot fade in short term in the concrete productions where good quality inorganic pigments are used, however the colours can rarely fade slightly in long term due to dust and contamination because of air pollution and very intense sun raids. We will mention about efflorescence and decomposition problems in the coming chapters.
Low oil absorption
The oil absorption rate of a good quality pigment should be low. As a result of this low rate, there constitutes only very little spaces in the concrete and thus prevents the weakening of the concrete.
Low water absorption
The Water Absorption particularly in the pigments with a needle structure is much. Excess use of water in the mixture reduces the binding power of the cement and causes the concrete to weaken.
Purity
The purity of a pigment is a most important factor which affects the quality. The purest pigment you use the best results you obtain.
Factor of Raw Materials and Pigments in Concrete Colouring Process
A pigment used for colouring purpose causes several effects on the concrete depending on the quality of the used pigment. We have mentioned about the properties of a good quality pigment and the effect of it on the concrete before, in choosing good quality pigment selection. Attention should be paid to the fact that even though some consumers who use bad quality pigments prefer to use more pigments so as to get the colour they desire, the inorganic pigments that are used more than 5% in quantity do not increase the colour and they also prevent the binding power of the cement and cause the concrete to be crumbled. Thus, all the production goes waste and there happens a loss of 100%. You can use SUN inorganic pigments successfully as a cement colouring substance in the production of concrete elements by spending a minimum cost and having a maximum quality.
Cement Colour in Concrete Coluring Process
Cement which we mentioned at the beginning among the raw materials used in concrete production is one of the factors affecting the colour result in pigment usage. The existing cements in the market can be in several different colours some of them due to cement production techniques, and some of them due to the raw material of the cement. Contrary to what is known, the colour of the cement can be green, light yellow and brown besides gray. That the colour of the cement used is gray does not mean that all of them are in the same tone. Some of them can be dark gray while some of them can be light gray and this may not be noticed at first glance easily.
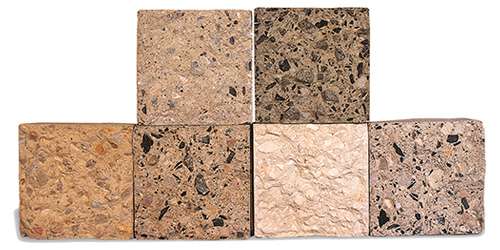
The Structure and Colour of the Agrega as a Factor in Concrete Coluring Process
Another factor in concrete colouring process is the used agrega. The agrega may be thick or thin, light colour or dark colour. The use of thick gravel both deteriorates the surface of the product and the appearance of the colour. Using dark colour sand and stone chips effects the colour power of the Pigment. To use light colour thin gravel is the best production method to give best solutions.
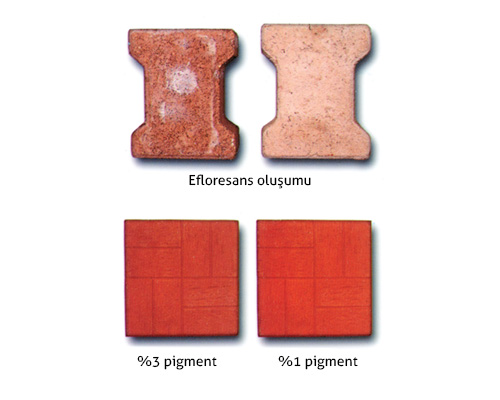
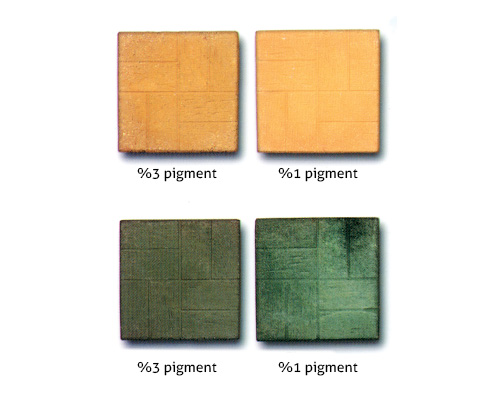
Sun Inorganic Pigments
The first product our company is proud to introduce to you, ie. to our valuable customers, is SUN SDR 333, which is a synthetic iron oxide pigment with a brick-red colour. Thanks to its power of colouring and resistance against exterior factors, you will get perfect results and thus become addicted to use it in your manufacturing processes. The colour factor will no longer be a problem in the production while use SUN SDR 333, and this product will provide you and your products to serve as a source of satisfaction for your customers. The second product that we will introduce you is SUN SDY 412, which has a lemony yellow colour and is a synthetic iron oxide pigment. SUN SDY 412 is a product which you will be very fond of and which will be accepted very quickly in the manufacturing (products with cement) sector.
Another sample of quality is SUN SDB 140 which you will use with great satisfaction. It is a real source of black colour. Its superiority in power of colouring cannot be debated, and it is a pigment which removes the notion "colour fading" from the dictionaries. Another pigment you will be introduced to is SUN SCG 566 which is brown in colour and is a perfect product to enable you to perform your manufacturing processes safely and with pleasure.
If you want the best tone of green, then what you searching for, is SUN SCG 228. Providing you with the best green which you can use in your concrete productions is both a means of pleasure for us and a source of excitement for you.
Where are Sun Inorganic Pigments Used?
SUN inorganic pigments are used in the following production areas with great success:
- Combined with the usage of cement. Concrete parquet, tiles floor furnishing, wall covers, concrete roof tiles etc.
- Production of synthetic colours
- Production of rubber
- Production of printer's ink
- Production of glass
- Production of ceramics
- Other productions of inorganic structure
Way of Use the Sun Inorganic Pigements
When you use SUN inorganic pigments we advise you to be careful about the following points so as to get the best results: The ratios given as a measure are according to the amount of cement;
- The best result is obtained when you use white cement combined with light colour agrega, when you use SUN inorganic pigments. Whilst the production under these conditions, it should be used in a ratio of minimum 0.5% and maximum 2.5%.
- When using black cement and light colour agrega, the ratio of SUN inorganic pigments has to be minimum 1% and maximum 3%. This will ensure you to get the desired colour tone.
- The maximum rate to be used for SUN inorganic pigments is 5%. A usage above this ratio will not cause a better colouring, but a waste and an increase in cost.